Fast color change
Fastest color change times increase production efficiency and save the environment
Fastest color changeover times increase production efficiency and protect the environment International extrusion experts have spent decades working on enhancing production efficiency by reducing the relatively long color or material changeover times at the extrusion heads of blow molding machines.
Faster changeovers not only increase your production efficiency by maximizing production times, but also cut your operating costs. What’s more, there is a significant saving in resources as the consumption of materials and energy is reduced in the time saved.

Reduced costs
Lower operating costs
Higher productivity
More efficient production thanks to shorter changeover times
Time saving
Up to 75% quicker color changeover for mono-layer applications with uncoated heads
More sustainable production
Saving of resources by up to 75%
RapidXchange - 100% color changeover saving up to 75% in time and materials
The key to making fast color changeovers lies in the design of the flow channels. Deposits build up here in “dead water areas” during the extrusion process and take a long time to purge out. Dead water areas are sections in the flow channels where flow speeds are low during purging.
With the RapidXchange technology, we have developed a way to reduce the purging process by up to 75% through rheologically optimized flow channels. The groundbreaking results were achieved in comparison with uncoated heads in mono-layer applications.

100% color changeover with 35mm die tooling after only 20 minutes
Time requirement and material consumption in two examples
Depending on the diameter of the parison, color changeovers with RapidXchange technology can be achieved in just 10 minutes.
The information listed below refers to the color changeover of a mono-layer application.
60mm die size
Material consumption = 15 kg per cavity
100% color changeover after approx. 20 minutes
35mm die size
Material consumption = 6 kg per cavity
100% color changeover after approx. 10 minutes
100% cleaning is the aim. The last 2% in particular is the most time-consuming.
In traditional melt distribution systems, color and material residues accumulate in areas where the flow speed is too slow to purge them out quickly and efficiently. This is often referred to as the crucial 2%, which causes long changeover times.
The RapidXchange technology developed by Kautex Maschinenbau System GmbH significantly improves the flow properties of the flow channels to such an extent that the last 2 % of the deposits is purged out of the system in next to no time.

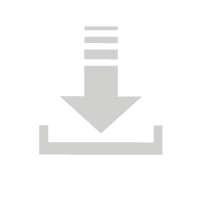
Downloads on this topic
You can find brochures, pictures and videos in our media center.
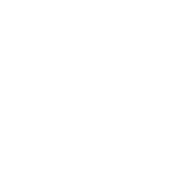
Our RapidXchange technology is available on our WT and ZVT extrusion head series
The extrusion heads have been designed for packaging applications and have been put through its paces to ensure highly efficient production. Investment costs are also lower thanks to their compatibility with common head tools made by other manufacturers.
The heads of the WT series are designed for both two-layer DeCo and three-layer ReCo applications and are available with up to 16 cavities. The extrusion diameters range from 35 to 600 mm. Kautex’s own electrical wall thickness control system (EWDS) ensures that service support can be provided as quickly as possible, and that spare parts are available at very short notice.

Enhanced production quality and flexibility
Using specially developed and optimized parison forming units not only reduces the time needed for color changes, it also ensures particularly uniform all-round distribution, guaranteeing even better production quality.
The more uniform the all-round distribution, the thinner the walls of an article can be. It is no longer necessary to compensate for weak points through the complete wall thickness. The article weight can thus be reduced and the quality of the product can be increased at the same time.

Die heads
Kautex has been producing die heads for decades. We develop, realize, and optimize our machines together with all extrusion blow molding components, and we provide a large bandwidth from mono to multilayer extrusion.
K-Technology
Your added value for “smart” production solutions of hollow plastic products. With K Technology, Kautex customers achieve the perfect melt, the most homogeneous distribution, and seamless production sequences.

All contacts quick and easy
We are here for you.
Service Hotline
You can reach us by telephone at