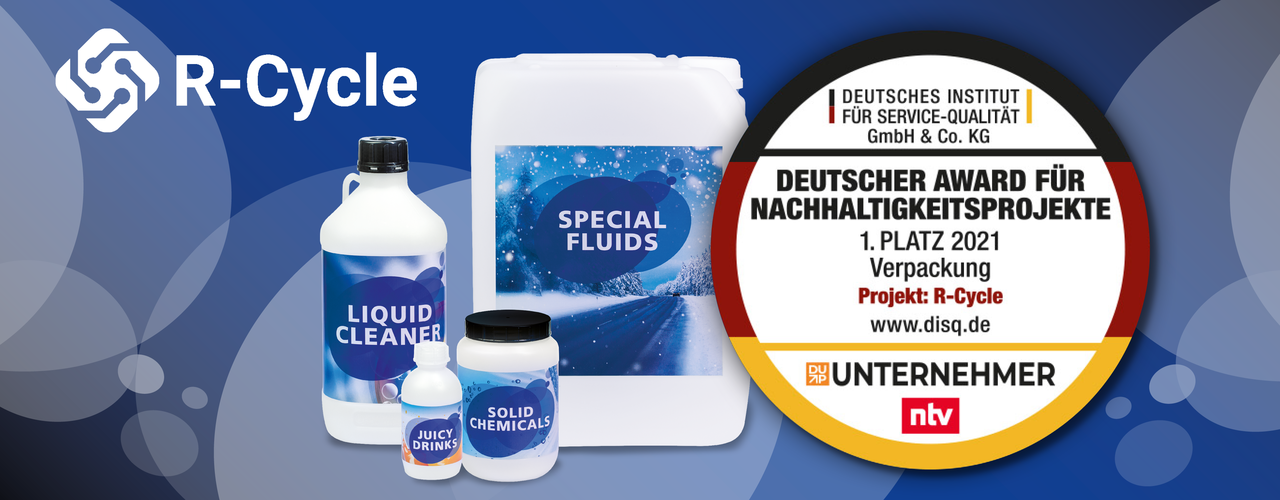
We are fulfilling the needs of the Digital Product Passport for the future circular economy - out of the extrusion blow molding perspective
Together with plastic raw material supplier Braskem, plastic packaging manufacturer KautexTextron and Netherlands-based recycling specialist company Morssinkhoff Plastics, Kautex Maschinenbau has launched a second R-Cycle pilot project “Smart digital watermark packaging in Blow Molding”.
The project objective is to make further contribution to the future functional circular economy by fulfilling the needs of the Digital Product Passport.
How do we improve the recyclability of packaging in extrusion blow molding?
In order to make this project cover as many application areas as possible in consumer packaging, our target products are:
- 250ml beverage bottle
- 1L cans for solid detergents
- 3L gripper bottle for household chemicals
- 20L jerrycan for chemicals and special fluids.
All articles are made of PP or PE, produced in mono-layer design and manufactured with extrusion blow molding processes. The product caps and lids are also made of polyethylene or polypropylene.
The Mono-layer design and the usage of the same material for packaging components improves a lot the recyclability of the packaging.

How do we store properties of plastic packaging for the Digital Product Passport?
R‑Cycle provides an open and globally applicable standard for the automated data transfer process.
All recycling relevant information - the manufacturer, the types of plastic contained, the content of recycled and biobased material, and details regarding the packaging’s application in food or nonfood area - has been recorded by the Kautex blow molding production platform. During the production process all data was sent and saved on the R-Cycle server with GS1 global tracing standard to fill the formal needs of the Digital Product Passport.
A marker is applied here to identify and read that information in further processes until the waste sorting system.
R-Cycle is open to a range of different marking technologies for example the QR-technology or digital watermark code.

In the second step of the new pilot project, a digital product passport is generated for each article in form of digital watermarks.
These marks, which are invisible to the human eye and duplicated across the entire surface of the packaging label, are the important key to link information to the R-Cycle database. The digital watermarkers contain all relevant information which are mentioned before and mandatory for the Digital Product Passport.
With this technology, waste sorting systems with an appropriate detection system can identify fully recyclable packaging. In the end, this provides the acquisition of high-quality materials for a truly effective recycling system and ensure highest grades of recyclate.
Additionally, these codes can be read on any smartphone by each end-user by simply using the Digimarc app

How do we make the traceability in extrusion blow molding happen?

As part of the pilot project, the recycling relevant properties were collected on production platforms of the customers and partners involved. It was sent to and stored on the R-Cycle server using a GS1 standard.
With this real-time transmission, the data is immediately accessible along the whole value chain.
Kautex’ main development of the pilot project is the data collection system “R-Connector”, which functions as link and interface between the extrusion blow molding production and the cloud-based R-Cycle platform.
By using the “R-Connector” in Kautex production solutions, all necessary production data will be recorded, analyzed, and uploaded to R-Cycle serve in real time. This is increasing production efficiency and transparency significantly.
In this way, waste sorting facilities can identify fully recyclable packaging by using standard detection technologies. Most importantly, this open and globally applicable tracing standard is the key to obtaining high-quality recyclate for true recycling in the future.
Stay tuned for further updates on progresses about the Kautex pilot project.
R-Cycle Pilot Project #1
Working together with partners to promote sustainable recycling management
We follow our corporate vision and develop "smart" production solutions for added value creating plastic products. This includes in particular sustainability-oriented solutions.
At the start of 2020 the European Union published its Action Plan for the Circular Economy to ensure that plastic packagings are traceable in the future and thus more recyclable. This is also tremendously important issue for Kautex Maschinenbau. For this reason we have committed to the R-Cycle initiative, in which we join together with significant partners in the plastics sector, to promote this objective with passion and ambition.
R-Cycle Pilot Project #1 is the open and globally applicable standard for the tracing of plastic packagings throughout the life cycle. The aim is to guarantee recyclability through complete documentation of all recycling-relevant packaging properties on the basis of established technologies.
R-Cycle Pilot Project #1 fulfills one of the most important prerequisites for the recycling of plastics as marking makes the packaging identifiable. The complete value chain can be traced right back to the raw materials used via a cloud-based database.
R-Cycle Pilot Project #1 officially started in June 2020. The plastics machinery manufacturers Reifenhäuser, Arburg, Brückner Maschinenbau and Kautex Maschinenbau are taking the lead in the project at present, together with the IKV Institute for Plastics Processing at RWTH Aachen University. We receive support for our work from GS1 Germany, a neutral center of excellence and service center for optimization of cross-company business processes throughout the value chain.

For further information please refer to: www.r-cycle.org

R-Cycle Pilot Project #1 Kautex Maschinenbau / Braskem / Morssinkhoff / Kautex Textron
Recycling-friendly, traceable blow molded bottle made of sustainable materials
Together with plastic raw material supplier Braskem, plastic packaging manufacturer KautexTextron and Netherlands-based recycling specialist company Morssinkhoff Plastics, Kautex Maschinenbau has launched the R-Cycle pilot project “Smart sustainable packaging in Blow Molding”.
This combination of project partners maps the entire value chain from plastics production to processing and recycling. The project objective is to develop a recycling-friendly and traceable bottle made of sustainable materials.
The target product has been defined for a first step as a 1-liter bottle made from two different HDPE materials: One bottle is made from Braskem’s I’m greenTM biobased PE, produced from sugar cane (white bottle), The second bottle is made from Braskem’s I’m greenTM Recycled PE, a material made from recycled plastic waste (grey bottle).
Both bottles are produced with extrusion blow molding processes, using a machine from Kautex Maschinenbau that offers ideal conditions for processing new types of plastics and is integrated with coding and marking technology via digital interfaces.
Both bottles, produced with both sustainable materials, are 100% recyclable. By this, they can be returned to the recycling loop and granulated into a high-quality recycled material.
The tracing technology behind the R-Cycle Pilot Project #1 is based on GS1 standards. In the first step, we are using QR codes as marking technology for the bottle. In addition, other possible marking technologies will also be tested during the project.

Energy efficiency
The outstanding efficiency of the all-electric extrusion blow molding machines is confirmed by the latest test based on the Euromap 46.1 standards. Several Kautex machines of the KBB series achieved the best energy efficiency classification 10.
Sustainability
As mechanical and polymer engineers, it is essential that we ask ourselves how we can contribute to the sustainable handling of plastics. This sustainability is best achieved with a fully functioning recycling system.

All contacts quick and easy
We are here for you.
Service Hotline
You can reach us by telephone at